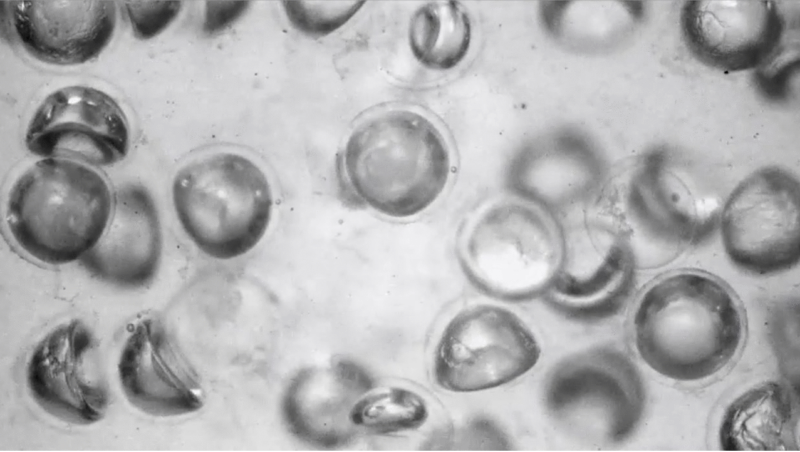
Building a robot that could pick up delicate objects like eggs or blueberries without crushing them took lots of control algorithms that process feeds from advanced vision systems or sensors that emulate the human sense of touch. The other way was to take a plunge into the realm of soft robotics, which usually means a robot with limited strength and durability.
Now, a team of researchers at Harvard University published a study where they used a simple hydraulic gripper with no sensors and no control systems at all. All they needed was silicon oil and lots of tiny rubber balls. In the process, they’ve developed a metafluid with a programmable response to pressure.
Swimming rubber spheres
“I did my PhD in France on making a spherical shell swim. To make it swim, we were making it collapse. It moved like a [inverted] jellyfish,” says Adel Djellouli, a researcher at Bertoldi Group, Harvard University, and the lead author of the study. “I told my boss, 'hey, what if I put this sphere in a syringe and increase the pressure?' He said it was not an interesting idea and that this wouldn’t do anything,” Djellouli claims. But a few years and a couple of rejections later, Djellouli met Benjamin Gorissen, a professor of mechanical engineering at the University of Leuven, Belgium, who shared his interests. “I could do the experiments, he could do the simulations, so we thought we could propose something together,” Djellouli says. Thus, Djellouli’s rubber sphere finally got into the syringe. And results were quite unexpected.
The sphere has a radius of 10 mm, and its 2-mm-thick silicone rubber walls surround a pocket of air. It was placed in a container with 300 ml of water. When the pressure in the container started to increase, the sphere, at 120 kPa, started to buckle. Once it started to buckle, pressure remained relatively steady for a while, even though the volume occupied by the fluid continued dropping. The liquid with a sphere in it did not behave like water anymore—it had a pronounced plateau in its pressure/volume curve. “Metafluids—liquids with tunable properties that do not exist in nature—were theorized by Federico Capasso and colleagues, who wanted to achieve a liquid with negative refractive index. They started with optics back then, but looking at the behavior of water with this rubber sphere in it, we knew what we had was a metafluid,” says Djellouli.
AdvertisementMixing programmable fluids
Putting a single rubber sphere in the water was just a starting point. “I always had this idea in the back of my head: Like, what would happen if I put in a lot of them?” Djellouli told Ars. So, his team started to experiment with different sizes and numbers of the spheres in the medium and using different mediums like silicon oil. “You can tune pressure at which the spheres activate by changing their radius and thickness of their walls. When you make the spheres thicker, you need more energy to make them buckle and thus the activation pressure will be higher,” explains Djellouli.
There are other parameters that can be changed to program desired properties in the metafluid. These include the volume fraction—basically how much of the total fluid’s volume is taken by the spheres—and the structure of the spheres, as the fluid behaves differently when you put spheres with different sizes and thickness in it. You can also tune this by using mixtures of spheres with different properties. “If the variation in size and thickness of the spheres is very tight, you are going to have a very flat plateau of pressure when they activate. If you have a wider distribution, the transition from all unbuckled to all buckled will be smoother,” says Djellouli. Using different mixtures of spheres also enables multiple plateaus at different pressures in one fluid. “This way you can precisely tune the pressure/volume curve,” Djellouli adds.
By tuning those curves, his team managed to build a smart hydraulic gripper that works without the need for sensors or control systems.
Self-controlled robots
The goal for the gripper was to grab and hold three objects—a water bottle, an egg, and a blueberry—without crushing them. The basic design was very simple: one static finger and a second that opened and closed the grip based on the motion of a hydraulic piston. “Let’s say I want to give this actuator control but without me doing any control, and I want it to grab many different objects that vary in size, weight, and fragility,” says Djellouli.
His team started by doing this experiment with plain water and air acting as the hydraulic fluids driving the piston. It turned out there was no single volume of hydraulic material that would allow the device to grab all of them. Too little and it wouldn’t close on small objects.
“In this scenario you need to spend some fluid volume to reach the object first,” Djellouli explained. This reach volume was the highest for the blueberry, the smallest object, and the lowest for the bottle, the largest of the three. “When the gripper gets in contact with the object, it stops moving, and adding more fluid to the system starts to increase pressure to the point your object is crushed,” Djellouli said. “But with the metafluid we could do this. We tuned it to reach and hold all the objects without crushing them,” says Djellouli. His team introduced two plateaus in the metafluid that enabled the gripper to reach and hold the blueberry but kept the pressure in the safe range while grabbing the bottle and the egg.
The same trick can be used to introduce some degree of intelligence to otherwise crude and simple robots. “We can make hydraulic actuators soft and self-controlled. The fluid itself is doing all the control for us, so we don’t have to control the robot from the outside,” he adds.
AdvertisementSmartening up hydraulic grippers is just one of the talents of Djellouli’s metafluid. Many more came to light when the team started to make the spheres smaller, taking their size down to micrometer scale.
Optics and smart shock absorbers
“On the face of it, you could argue we didn’t need to make the spheres small. One of the professors told me miniaturizing them was not necessary because it would take lots of time and bring little added value,” Djellouli claims.
But it turned out there was added value. “In one of the experiments we noticed that when the pressure was low, the fluid was opaque, but when you activated the shells, it turned transparent,” Djellouli explains. This effect was discovered when the team put micrometer-scale spheres made with polydimethylsiloxane (PDMS), a transparent elastomer, in PDMS oil. “In an unbuckled state there was a high volume of air in the fluid. It was opaque because air and PDMS have different refractive indexes. But when the spheres buckled, the volume of air became very low, and the buckled spheres took a shape similar to what you find in contact lenses, which made the fluid transparent,” explains Djellouli.
But miniaturizing the spheres led to even more profound discovery. “We could tune the fluid’s rheology,” Djellouli said, referring to how smoothly it flowed. The team noticed that a fluid with compressed spheres flowed faster than one with non-activated spheres, even when driven by the same pressure difference between the input and outlet.
This opens a way to building things like intelligent shock absorbers that can change their characteristics. “Impacts and amplitude of the shock can be translated into pressure, and based on that you can tune the rheology depending on the impact that you are having. I think this can be done. If companies making shock absorbers think this could be a good system, we’d like to meet them and see if we can work with them,” says Djellouli. “But when it comes to rheology, now we are just scratching the surface,” he adds.
Nature, 2024. DOI: 10.1038/s41586-024-07163-z